Uptime when it matters most
Flexco’s FXC steel cord belt fastening system is keeping conveyor systems up and running across Australia.
Steel cord conveyor belts are put to use in only the heaviest of applications, such as high-tension applications like moving hard rock and heavy metal.
But the sturdy nature of such equipment poses logistical challenges when it comes to maintenance. In the event of belt damage or pulling a new belt onto the conveyor system, few timely options have traditionally existed for splicing steel cord belts.
Until now.
Flexco’s FXC steel cord belt fastening system can be installed immediately to get a conveyor system up and running as quickly as possible.
Mine sites would ordinarily have to wait for a vulcanised splice on the conveyor belt, which can delay operations for days. With the FXC steel cord belt fastening system, however, the belt can be temporarily spliced in just hours until a vulcanised splice can be installed.
“The FXC system is a first-of its-kind mechanical belt fastener for steel cord belts,” Flexco product manager – HD mechanical belt fasteners Franklin Moore told Australian Mining.
“Nothing like this exists on the market right now and we are incredibly excited to share our patented design with the world.”
Flexco’s testing has demonstrated that four workers are able to splice a 72-inch-wide steel cord belt in just 4–6 hours.
“The stress of waiting to get a belt back in operation is one thing, but we also know how detrimental this downtime is to the site’s bottom line,” Moore said.
“While this is a temporary splice, it bridges the gap until a permanent vulcanised splice can be installed.
“The FXC can be kept on hand as an insurance policy so when faced with unplanned downtime, customers can respond immediately.”
The FXC fastening system also enables quick and efficient belt pulling.
“Another option available with the FXC is that it enables sites to attach a new steel cord belt onto an existing one in order to string the new belt onto the system,” Moore said.
“Teams can prep the new belt end prior to shut down for minimal downtime when changing a belt, and a safety factor is calculated to give sites confidence when pulling the new belt on.”
Testing in this area has shown four workers can prep a 72-inch-wide belt for stringing onto a conveyor in three hours.
That means the FXC fastening system can manage the biggest challenges associated with steel cord conveyor belts.
“The FXC empowers customers to reduce the amount of downtime associated with steel cord belts, which are often incredibly important to a site’s production,” Moore said.
“Scheduling, transportation time, belt prep, installation and curing time of a typical vulcanised repair or replacements can take days, if not weeks.
“This downtime and lost production are extremely expensive, so we are giving these teams a new method for getting back up and running in just a few hours.”
Flexco also understands that steel cord belts come in all shapes, sizes and construction.
That’s why the company collects belt specifications from customers in order to create and deliver a customised FXC fastening system to suit a site’s specific needs.
Made from high-quality components, the FXC fastening system has been expertly designed and rigorously tested in different mining environments around the world.
“Flexco has been the trusted expert in mechanical fasteners for over 115 years, so it’s exciting to improve our customers’ efficiency in a whole new belting market,” Moore said.
“Leading the way with a mechanical fastener for steel cord belts has been exciting for the whole Flexco team, but the benefits it offers our customers is the most special aspect.
“The FXC has been welcomed into a variety of different industries around the world and the reception has been astounding.
“Flexco is proud to offer something that gives sites control over expensive and extended downtime.”
Source: https://www.australianmining.com.au/uptime-when-it-matters-most/
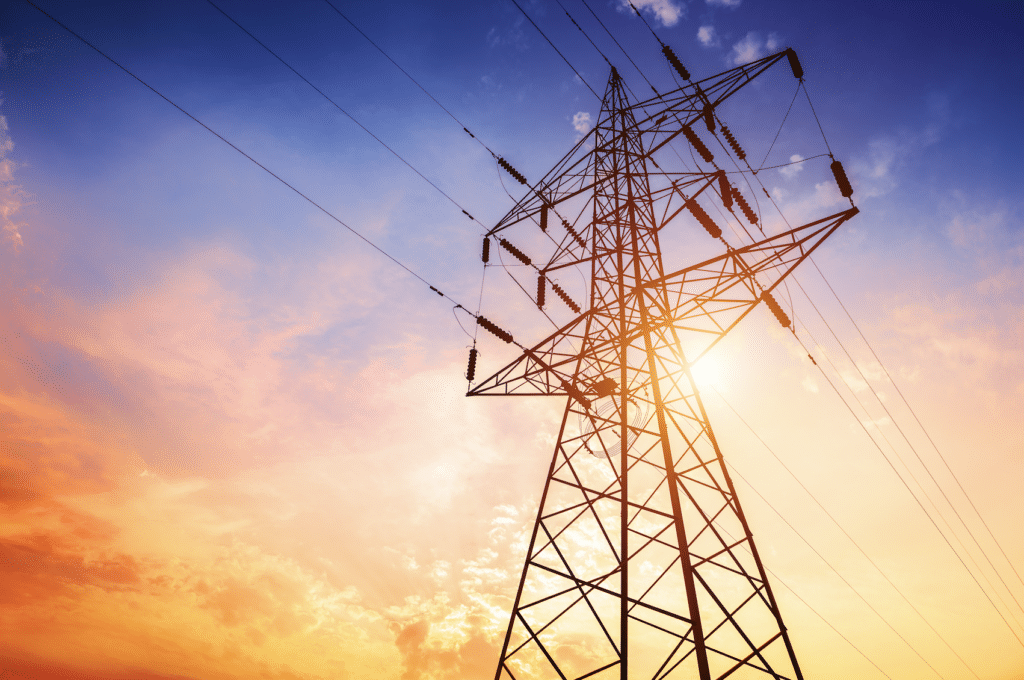
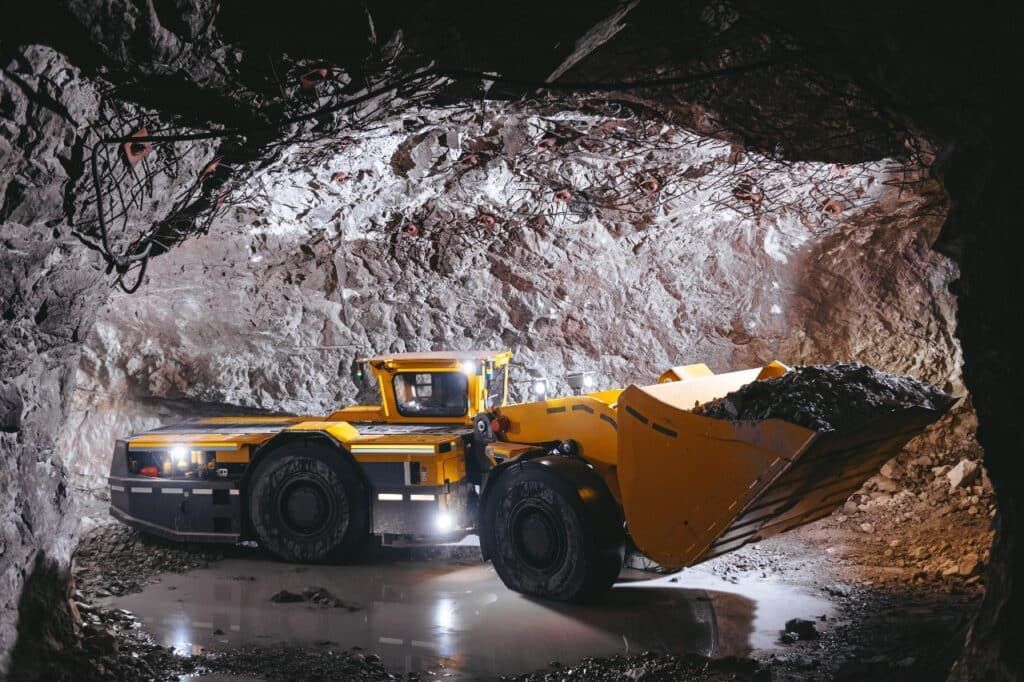
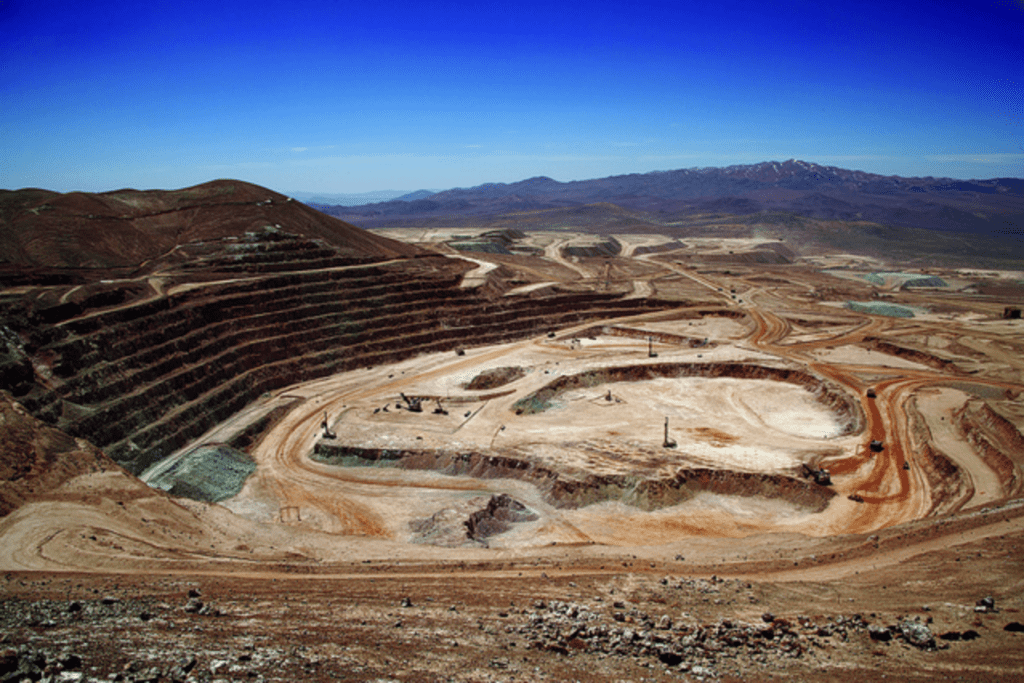