Tech-powered solutions to maximise field resources
Appian resources, energy and utilities account director Justin Grose explores how the company’s field service management solutions can address the unique challenges of the mining industry.
Running a mining operation is a highly complex task. Beyond exploration and production, miners now must navigate ESG, decarbonisation, market volatility and increasing operational risks.
With 24–7 operations across remote locations – often under harsh environmental conditions and with limited infrastructure – efficiency is key when coordinating and monitoring a dispersed workforce.
How can the mining industry simultaneously save time, increase productivity, reduce disruptions and downtime, and improve asset utilisation?
The Importance of field service management in mining
Field service management (FSM) involves coordinating field operations, managing work orders, scheduling tasks, and ensuring that field workers have the tools and information they need to perform their duties efficiently.
In the mining industry, FSM is vital due to the complexity of field operations, the remote locations of sites, and the heavy reliance on equipment and vehicles that require regular maintenance and monitoring to prevent breakdowns.
Efficient FSM ensures that complex tasks are meticulously planned and executed, worker safety is maintained, and operations run smoothly.
Field service challenges in the mining sector
The mining industry faces several challenges that can hinder effective and efficient field service management:
- Geographical dispersion: Mining operations are typically spread out over large areas, making it difficult to maintain direct oversight of workers. This dispersion complicates communication, supervision, and coordination
- Harsh environmental conditions: Miners work in extreme conditions, from scorching heat to freezing cold, which can impact both the workers’ health and the operational equipment. Ensuring the well-being of the workforce and the smooth functioning of operations in such environments is a constant challenge
- Safety and compliance: The mining industry is heavily regulated, with stringent safety and compliance requirements. Managing these regulations across multiple sites is complex and requires meticulous attention to detail
- Resource allocation: Efficiently allocating resources, including manpower and machinery is crucial in mining operations. Misallocation can lead to downtime, increased costs, and reduced productivity.
Enhancing field management with innovative technology
To address these challenges, mining companies are increasingly turning to technology that streamlines operational efficiency.
Mobile applications and digital platforms can revolutionise how field operations are managed.
With a large workforce operating from hazardous, remote sites, it is imperative for mining companies to stay connected with their on-site employees – communications which are completely dependent on mobile devices.
For example, BAI Communications Australia operates one of the most extensive broadcast networks in the world.
The company faced challenges with labour-intensive manual processes for managing site access, which required multiple phone calls, emails, and document sharing between staff and contractors.
To upgrade from manual to automated processes, and digitise and optimise Site Access Management, BAI created a digital prequalification application on the Appian AI Process Platform for all site visitors.
This significantly reduced processing time for access requests and improved safety and security procedures.
The mobile app developed for field staff allowed them to log in and out of sites, view faults and work details, and report hazards and risks in real-time.
The benefits of such digital solutions extend beyond improved safety and efficiency. Real-time visibility and tracking, roster and shift planning, workforce analysis, and time attendance are now more streamlined.
Integrated platforms facilitate seamless communication and coordination between the field and the central office, ensuring that tasks are completed efficiently, and issues are addressed promptly.
Real-time data and analytics provide a clear picture of field operations, enabling better decision-making and proactive management of resources and tasks.
Embracing digital solutions for optimal performance
Effective field service management is essential for enhancing productivity, ensuring worker safety, and improving customer satisfaction.
Leveraging digital solutions like Appian’s low-code platform can address the unique challenges of the mining industry by providing robust, mobile-enabled applications that streamline operations and provide real-time visibility into field activities.
By embracing these technologies, the industry can optimise their field operations, reduce costs, and drive growth.
Source: https://www.australianmining.com.au/tech-powered-solutions-to-maximise-field-resources/
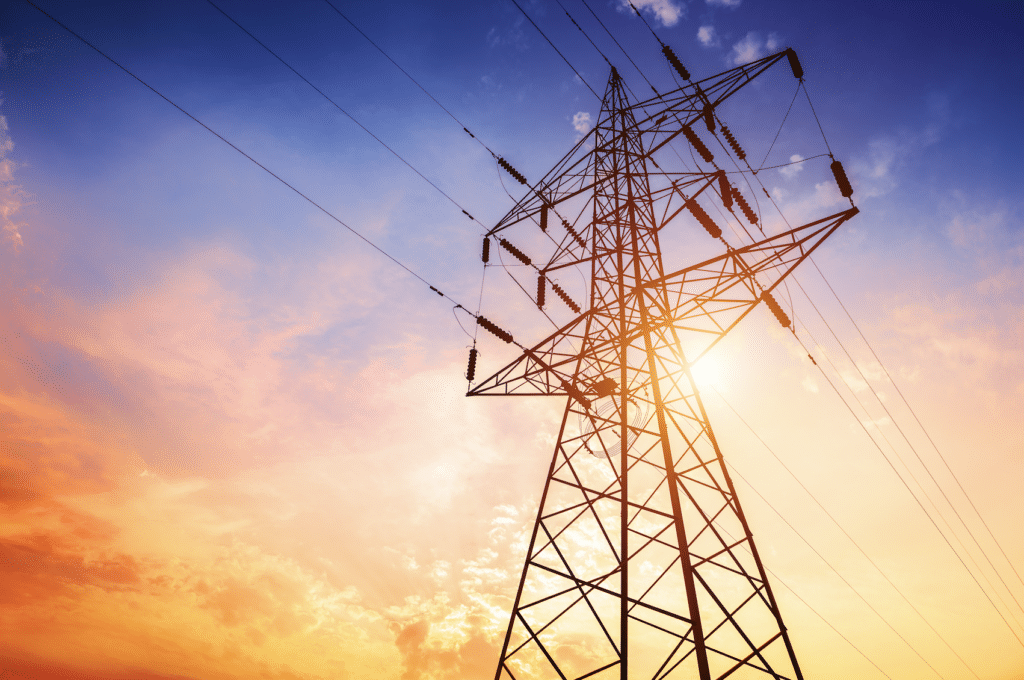
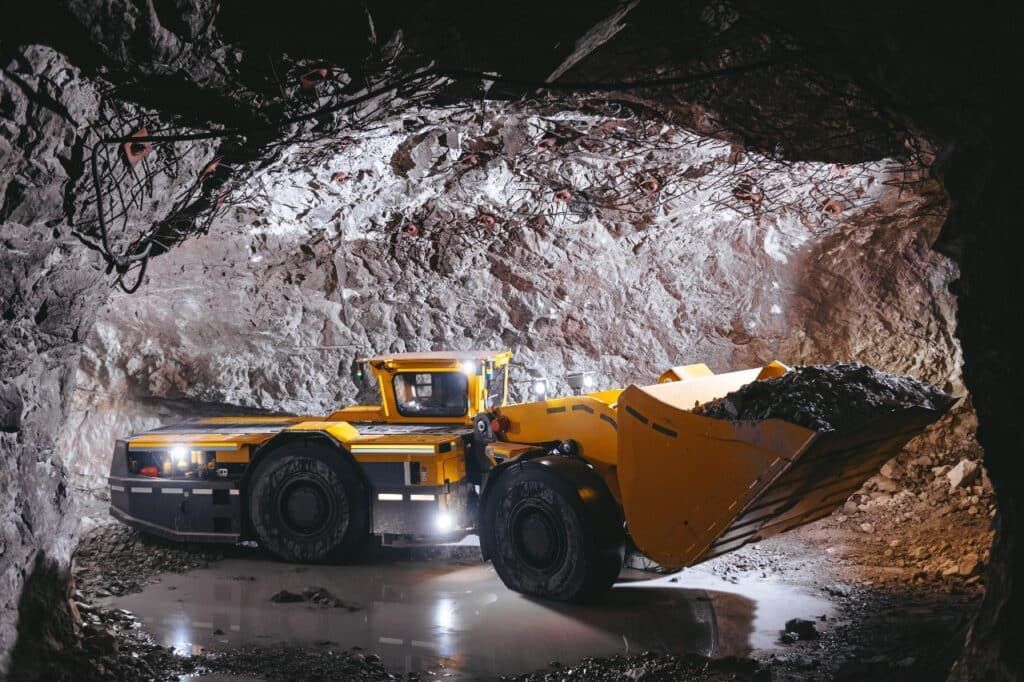
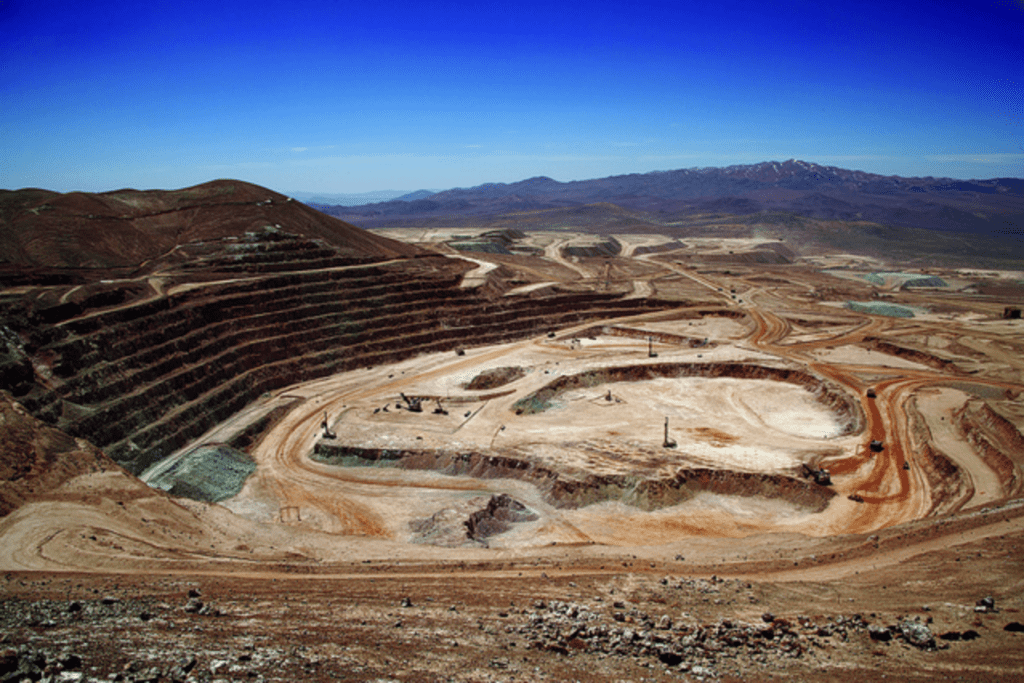