‘Taking the dirty out of diesel’
HYDI Hydrogen is helping to drive down carbon emissions for diesel-powered machines in the mining industry.
Mining companies have been facing pressure to decarbonise their operations from governments and stakeholders in line with the global shift towards net-zero.
As diesel usage is a significant contributor to Australia’s net carbon emissions, decarbonising heavy vehicles and other diesel-powered assets seems the logical place to start. In the mining industry, this is often achieved through switching to battery-electric assets.
But for an industry built on 24–7 operation, this is a complex and time-consuming process.
Among the challenges is the fact Australian mining operations are spread over vast distances, which makes introducing the necessary electric infrastructure expensive and logistically complicated.
In a similar vein, the switch between diesel and electric does not happen overnight. It involves trials and gradual implementation.
On top of everything, these diesel-powered heavy vehicles have operational lifespans beyond a decade, and in some instances can be rebuilt for an even longer life. Considering many companies have 2030 climate commitments to meet, this asset longevity puts them in a corner.
Mining companies must choose between replacing expensive-but-still-operational diesel assets with their electric counterparts or running out the life of these existing assets, possibly imperilling their decarbonisation goals as a result.
But what if there was a way to make diesel cleaner?
Such a transitional technology would allow mining companies to get the most out of their expensive diesel assets, ease the transition to electrification, and drive down carbon emissions at the same time.
The solution exists, and it’s called HYDI.
“HYDI is a hydrogen on-demand retrofit unit for large diesel engines which delivers immediate reductions in carbon emissions,” HYDI Hydrogen sales director John Wilson told Australian Mining. “HYDI reduces diesel usage by producing hydrogen as a fuel supplement.
“Where the units have been fitted to new and old engines, they are achieving up to 14 per cent diesel fuel savings.”
Every litre of fuel not burned saves an equivalent in carbon emissions. For larger operations, that means more fuel saved and a faster return on investment.
And in addition to reducing fuel consumption, HYDI makes diesel engines cleaner.
“Hydrogen supplements the diesel fuel to enable a stronger, cleaner and more complete combustion,” Wilson said.
“Independent testing has demonstrated reductions of 80 per cent in diesel particulate matter (DPM) and fewer carbon monoxide, carbon dioxide, and nitrogen oxide gases. Additionally, the fuel savings achieved from the HYDI unit further reduces greenhouse gas emissions.
“This makes for cleaner engines and a 60 per cent reduction of soot residue in the engine’s oil.
“It’s taking the dirty out of diesel.”
A cleaner fuel burn provides the engine with additional torque, improving productivity. Reducing DPM also improves air quality, which has environmental and safety benefits.
More than 300 units of HYDI have been deployed to date, with the majority applied to heavy haulage, drill rigs and generators in the mining sector.
The technology has received endorsement from ResourcesWA. Holcim Cement in collaboration with Scania are currently monitoring initial deployments on heavy vehicles in the Pilbara, with exciting performance data exceeding expectations on fuel and carbon emissions reductions.
It is a combination of intelligent design features that makes HYDI a perfect fit for the Australian mining industry.
“Our technology harnesses the benefits of hydrogen in an efficient, affordable and sophisticated way, and can be scaled to apply to multiple applications,” Wilson said.
“The unit is robust with a fully welded stainless-steel case to enable deployment in harsh environments.
“The unit does not store any hydrogen nor have any reliance on a pressure vessel, making it completely safe.”
In fact, HYDI doesn’t need any chemicals or additives to run – water is the only consumable. On top of safety and environmental benefits, this minimises service requirements for the unit.
Designed and built in Australia, HYDI is a simple solution to the complicated challenge of decarbonising a mining operation.
“In the absence of viable alternatives in terms of performance, refuelling infrastructure, and affordability, new diesel-powered vehicles will continue to be deployed for the foreseeable future,” Wilson said.
“While total fleet electrification is many years away, HYDI can be implemented today on diesel assets to immediately start driving down carbon emissions.”
Source: https://www.australianmining.com.au/taking-the-dirty-out-of-diesel/
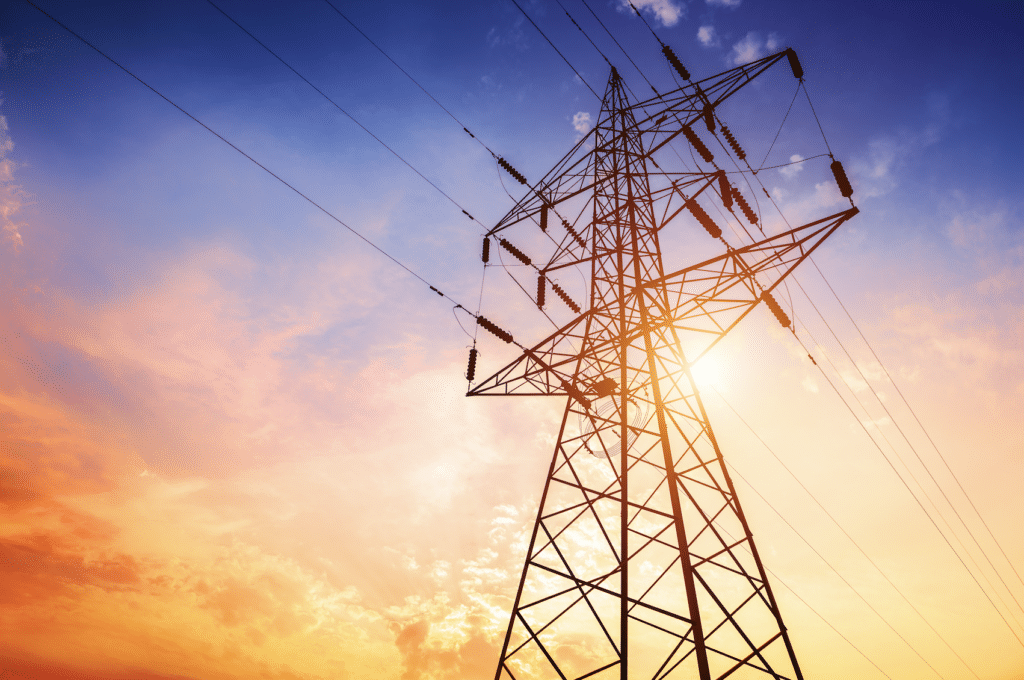
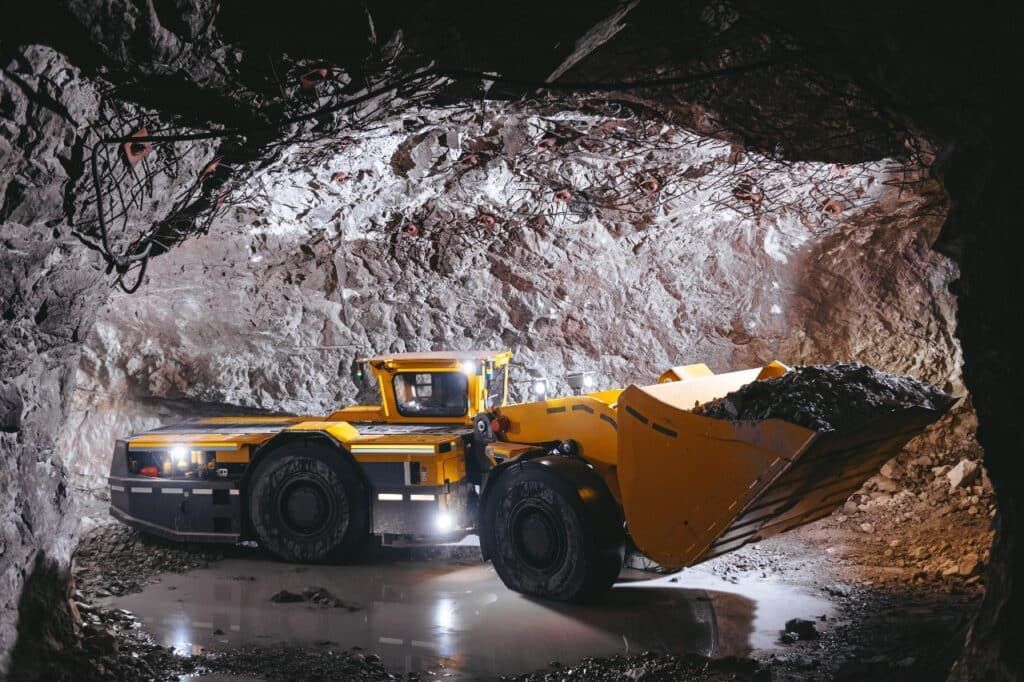
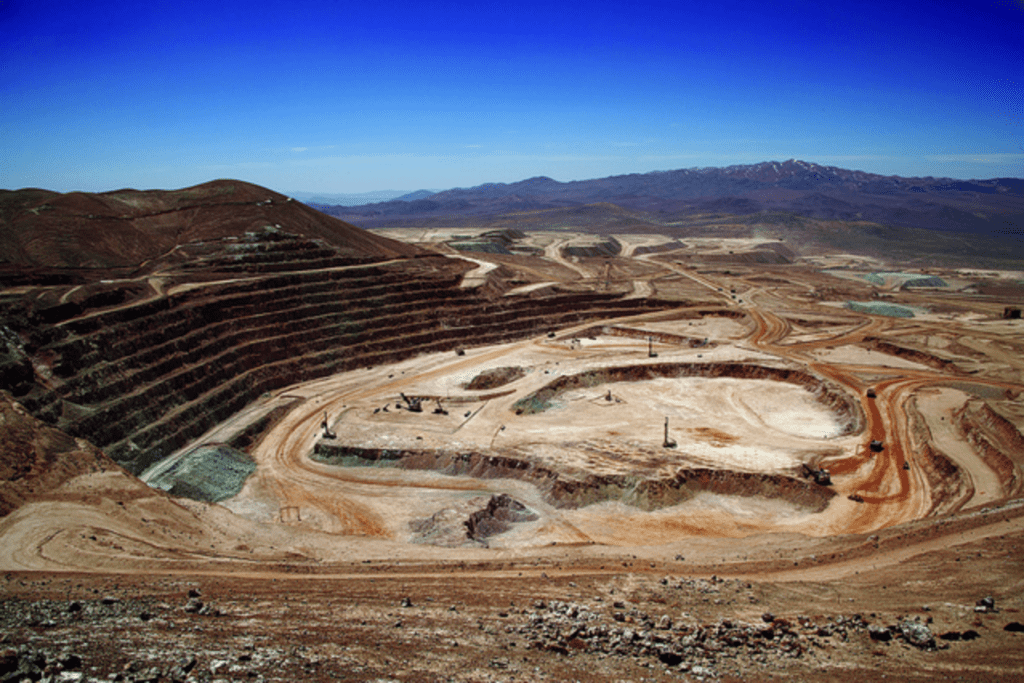