Smarter solutions start here
The Volvo Co-Pilot brings the next generation of mining technology to a mine’s doorstep.
As the demand for minerals and resources continues to grow, so does the mining industry’s responsibility to adopt sustainable technologies and practices.
The demand for efficient, economically viable solutions has led to remarkable innovations in the mining sector.
This includes the Volvo Co-Pilot, an intelligently designed interactive display enhancing mining operability.
Available as an option on select Volvo machinery, this technology is dedicated to equipping operators and site managers with a comprehensive toolkit and a wealth of information necessary for the establishment and maintenance of a highly sustainable, productive and profitable operation.
First released in 2016, Volvo Co-Pilot is fitted with all the latest technological advancements in driver assistance and safety features, setting the industry standard for excellence. It seamlessly works with Volvo Assist, a collection of functions comprising of dig assist, haul assist and load assist, providing real-time operational data for a responsive, harmonious and efficient operating experience.
When a SIM card is inserted, the Android-powered tablet display becomes 3G-enabled, facilitating seamless and wireless reception of software updates for the system.
The Co-Pilot system harnesses the potential of onboard machine data and high-precision sensors to streamline tasks, resulting in significant reductions in project completion times.
Co-Pilot’s user-friendly interface ensures operators can quickly initiate projects with just a few simple taps, effortlessly selecting the required job parameters.
Data collected through the Assist software programs can be captured in several ways. For example, it can be transmitted to the Cloud for access via an online portal, transferred to a flash drive, or printed via a small printer connected to the Co-Pilot interface through USB.
The logged information encompasses vital details such as work order number, customer name, loaded truck, load tonnage and the precise date and time of delivery, neatly organised in a spreadsheet format that seamlessly integrates into any customer’s enterprise resource planning system.
Notably, since Co-Pilot and the Assist programs are intricately woven into the Volvo machine’s electrical infrastructure, the system continually provides productivity data to Caretrack, Volvo’s telematics system.
Presented in a user-friendly format, customers can review details about their machine’s fuel consumption, utilisation percentage, and excessive idling to enhance operational efficiency.
This invaluable information empowers owners to identify potential training needs for operators and readily compare operating costs against production figures, both by machine and operator. These insights are a unique advantage, setting this integrated system apart from third party aftermarket solutions.
Safety has always been a paramount concern in the mining industry and Volvo Co-Pilot, with its intelligent systems and assistive technology, plays a vital role in enhancing safety standards on mine sites.
Volvo Co-Pilot not only simplifies the demanding tasks at hand, but also minimises workflow disruptions, enhancing onsite safety. The strategically positioned display reduces operator interactions with a reduced number of on-screen menus, enabling operators to stay focused on the task at hand.
This technology further promotes safety by promptly alerting operators, both audibly and visually, when predetermined operating limits are reached.
By employing Co-Pilot, the need for movement around the machinery and the necessity for additional on-site personnel are eliminated, resulting in an overall improvement in safety measures and operator autonomy.
With Volvo Co-Pilot, the operator can quickly and independently manage all operations with ease. The on-board display is intuitive enough to operate with minimal training and provides on-screen tips, optimising ease of operation.
Operators can also customise functions and targets in seconds and easily monitor the progress of their work with greater independence and confidence.
Sustainability is central to Volvo CE’s mission, and the Volvo Co-Pilot system is pivotal in promoting environmentally responsible construction practices.
By optimising machine operations and automating tasks, Co-Pilot actively contributes to reduced fuel consumption, lowering emissions and diminishing carbon footprints.
Furthermore, the system’s precise excavation and load-handling capabilities have the potential to minimise the need for rework, conserving materials, and further curbing waste production.
Volvo’s Co-Pilot monitoring features empower operators to make informed decisions based on data, resulting in additional reductions in fuel consumption and environmental impact.
By arming operators with tools that promote more efficient machinery operation, Volvo’s Co-Pilot is instrumental in fostering a mining industry increasingly committed to sustainability.
With Volvo’s commitment to science-based targets, the company continues to focus on environmental care and driving industry transformation to combat climate change.
Volvo CE leverages the extensive data gathered from operators worldwide to drive safety, uptime, and fuel efficiency enhancements that benefit both the present and future.
Integrating innovative digital technologies, such as Volvo Co-Pilot, streamlines the operators of Volvo machinery, promoting greater efficiency and concurrently reducing emissions, thereby enabling sustainable machine operation.
Volvo’s incremental improvements combine to deliver energy efficiencies across all types of Volvo construction equipment – a vital step forward in the world’s ongoing journey towards a carbon-neutral, sustainable future.
The global recognition of Volvo CE stems from its production of top-notch, safe, high-quality, and technologically advanced machinery. Telematics represents a significant stride in forming strategic customer alliances, complemented by additional productivity services.
For decades, CJD Equipment and Volvo CE have provided a range of premium construction machinery suited to Australia’s unique mining requirements.
Volvo and CJD deliver a range of productivity, fuel efficiency and safety solutions for a highly productive operation, ensuring machines perform at their best.
Source: https://www.australianmining.com.au/smarter-solutions-start-here/
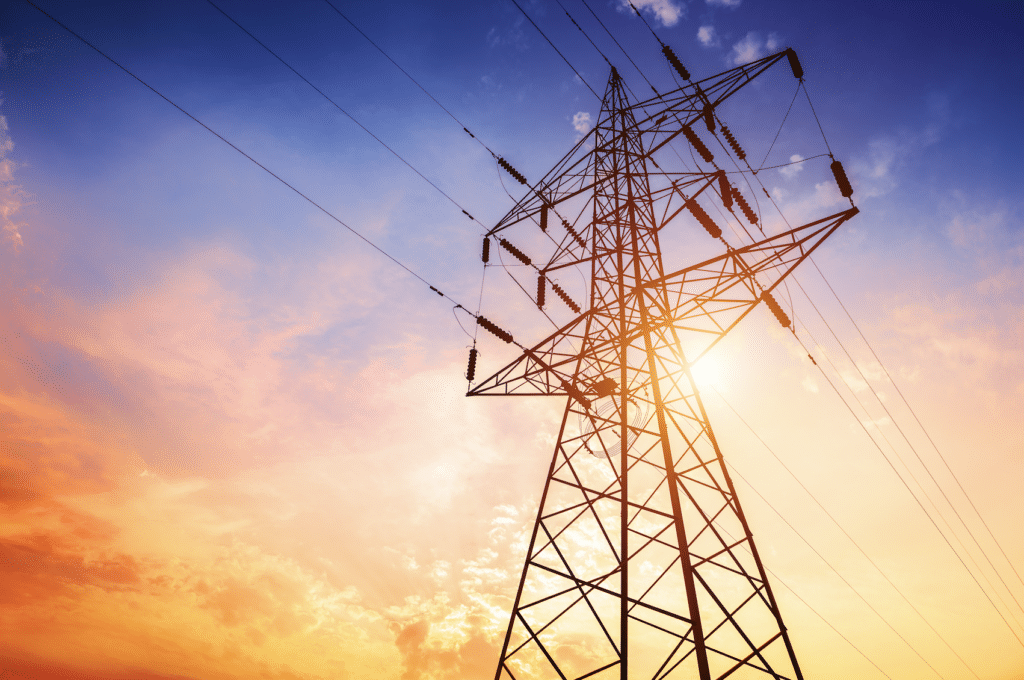
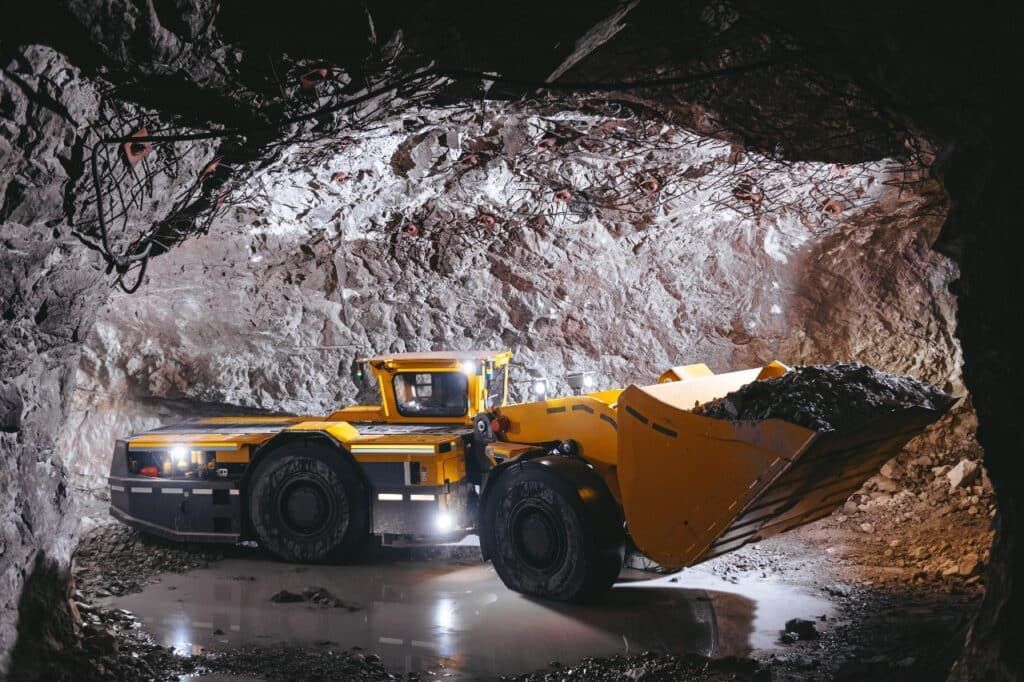
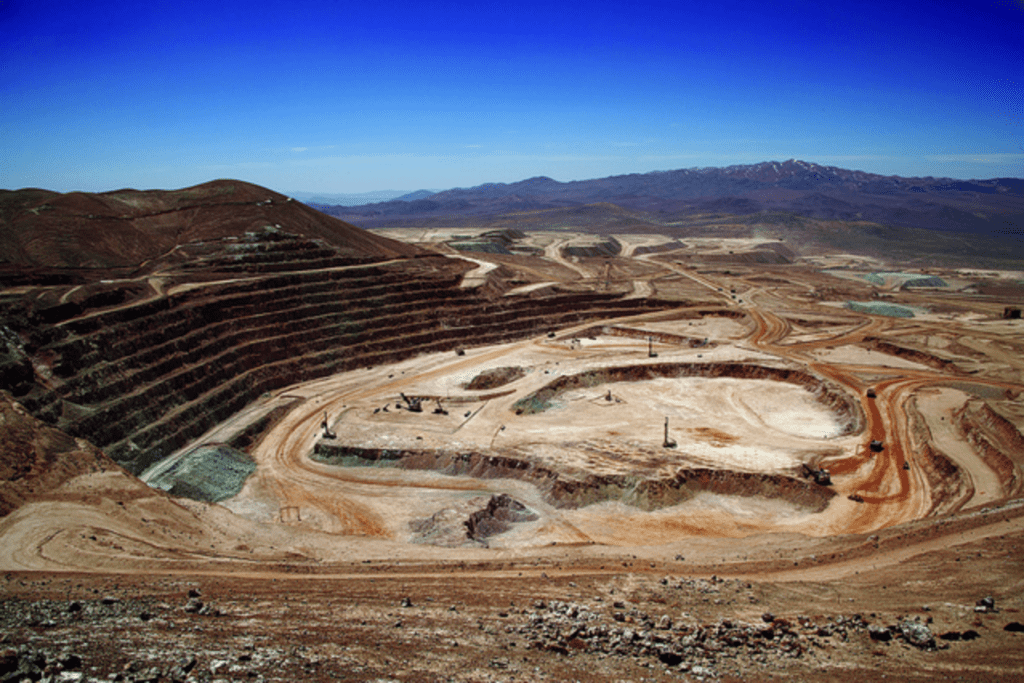