A bulletproof breaker
Backed by accessible servicing, Epiroc’s HB 2500 hydraulic breaker is as solid as a rock.
World-class original equipment manufacturer Epiroc is helping the mining industry dismantle its toughest problems with the HB 2500 hydraulic breaker for excavators.
The HB 2500 is expertly engineered for primary blast-free rock excavation and secondary rock breaking in surface and underground mines, as well as primary demolition of massive reinforced concrete structures.
Heavy hydraulic breakers are durable, efficient and highly adaptable products, making them extremely versatile for a range of tasks.
Breakers and Attachments Equipment Group, an Epiroc partner and the OEM’s largest Australian distributor, has sold more HB 2500s to the mining industry than it can keep track of.
“We get a lot of great feedback from our HB 2500 customers in regards to the productivity and the power that the breaker puts out,” BA EG national sales manager Nathan Parziani told Australian Mining.
“When it comes to a hydraulic breaker, it can only put out what it puts in, and Epiroc is industry leading in regards to end kilowatt input. The result is a hammer that’s durable, efficient and powerful.
“The HB 2500 is bulletproof.”
Intelligent design features help to set the HB 2500 apart from competitors. Epiroc’s patented Intelligent Protection System automatically adjusts the start-up and shutdown behaviour of the breaker during operation, making for easy positioning and maximum blank firing protection.
The HB 2500 also utilises the piston recoil energy to reduce vibration levels and improve performance. When combined with VibroSilenced Plus, which insulates the percussion mechanism and breaker box, these features significantly reduce noise levels and wear and tear from vibrations on the HB 2500.
The automatic lubrication system ContiLube II optimises the lubrication procedure, which significantly reduces maintenance.
And the optional active two-stage sealing system DustProtector II extends the service life of components and lowers grease consumption.
“The HB 2500 has a whole host of features, from the oval retainers to the encased tie rods to the fact that it has Helicoils instead of tie rod nuts,” Parziani said.
“Hydraulic breakers from other OEMs have exposed tie rods and tie rod nuts that create an extra point of leverage at the front head, weakening the hammer.
“Routine maintenance and failure are both a lot higher on those kinds of hydraulic breakers, because the power cell is under a lot more stress. The HB 2500 doesn’t have that problem.”
This was the experience of Local Mix quarry manager Steve Richardson, who was impressed with how well the HB 2500 was performing at his operation in Anakie, Victoria.
“We have two of the HB 2500, one of which we use for mobile crushing, mostly breaking up paddock rock on farmland,” Richardson said. “The other we have running at our quarry, breaking down oversize rocks and concrete too large for our pulveriser to handle.”
Richardson said Local Mix first made the switch to the HB 2500 after facing challenges with other OEM hammers.
“The hydraulic breaker we were previously using failed unexpectedly, and when we purchased a second, they didn’t have availability of spare parts,” Richardson said.
“So we turned to Epiroc’s HB 2500 – and soon purchased a second – and haven’t had any of those issues since.”
Richardson said maintenance on the HB 2500 has been a cinch, with BA EG technicians helping out with routine maintenance.
“We have had one overhaul on the hammer and it went really well. BA EG had all the parts available,” he said.
Parziani said the key to BA EG’s quick and reliable service is complete support from Epiroc.
“Epiroc has a strong presence in Australia,” he said. “What distinguishes us as a distributor is that the onus is often on our competitors to hold and support their stock, whereas we’ve actually got help here on the ground from Epiroc.
“What that translates to for our customers is great spare-part availability, dedicated service trucks, and experienced technicians.
“We also plan and work in with our customers to do shutdowns and routine maintenance.
“We’re involved in the day-to-day, keeping our equipment up and running for our customers.”
Epiroc is an esteemed name in the mining industry, and the HB 2500 is no departure from the OEM’s high standards in design and engineering.
Source: https://www.australianmining.com.au/a-bulletproof-breaker/
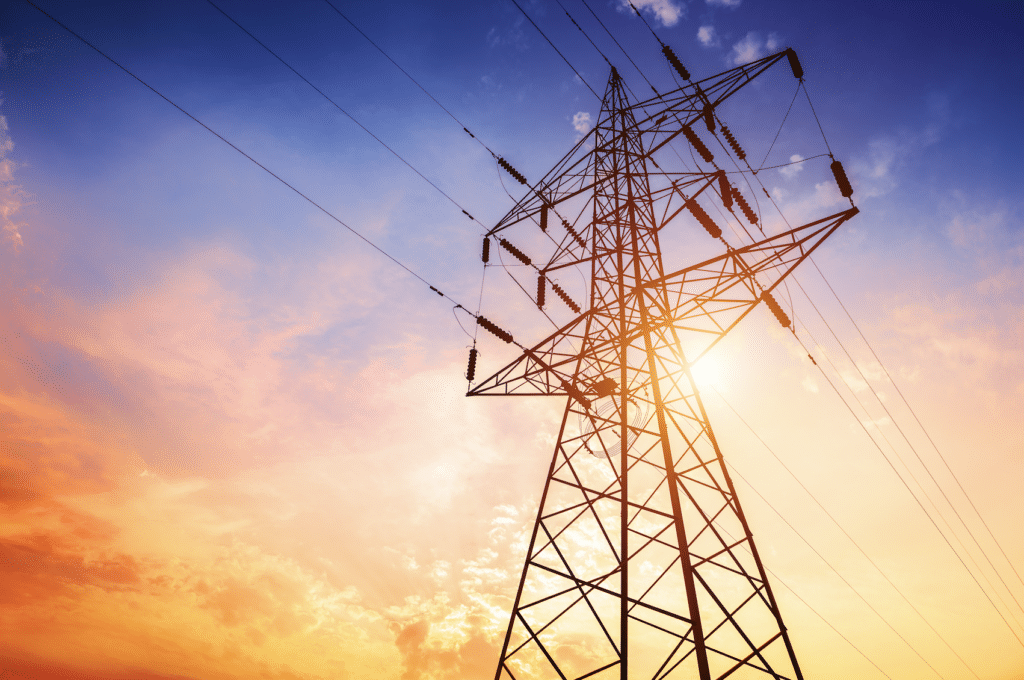
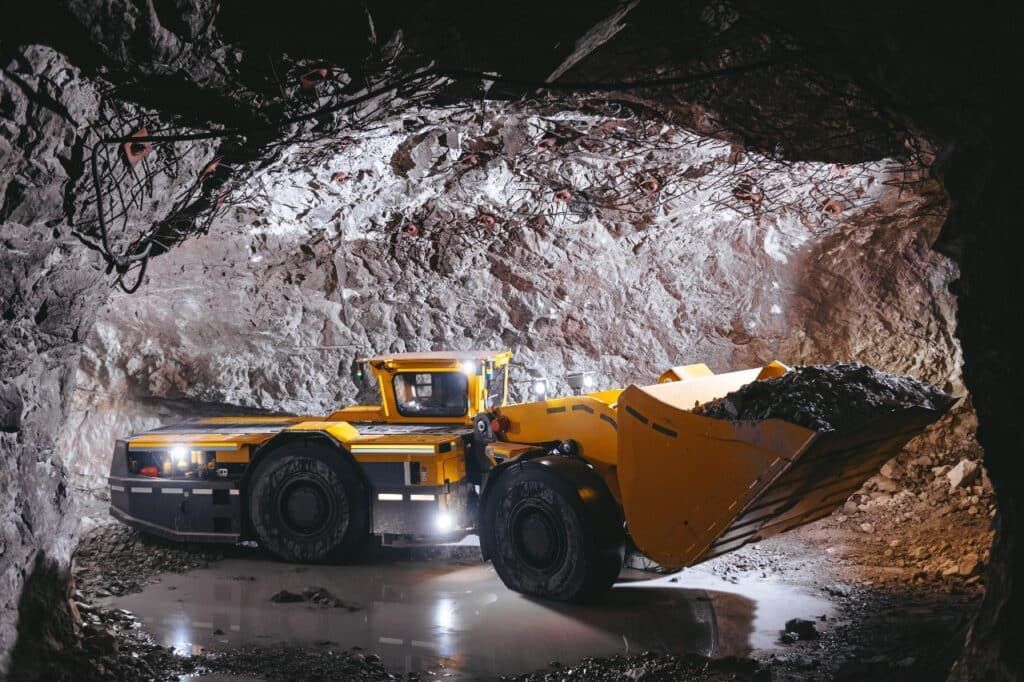
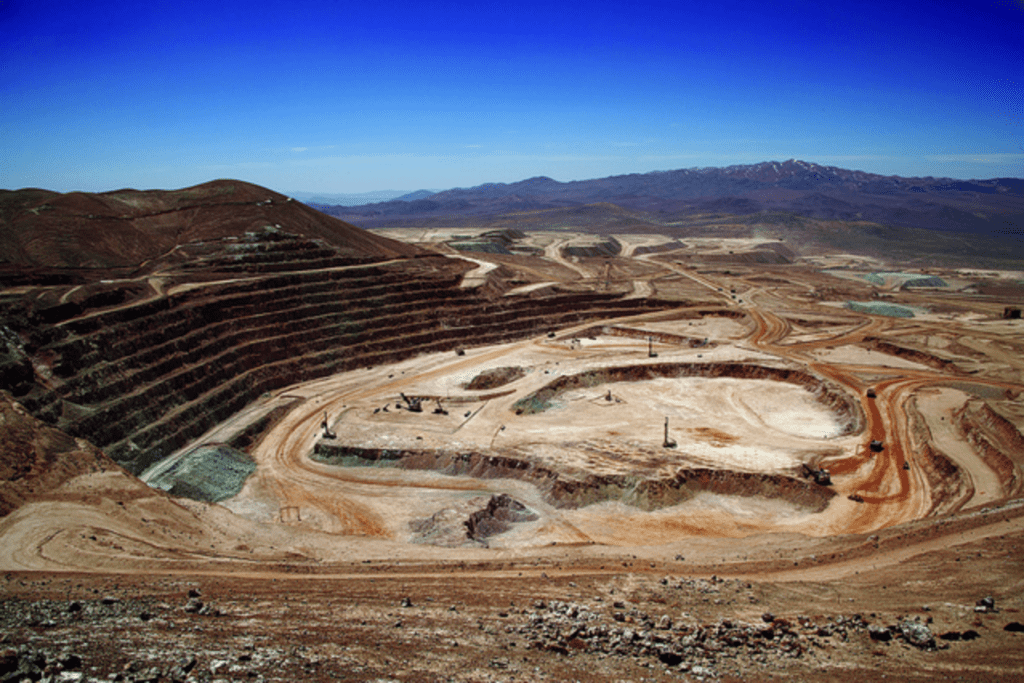